Состав и физические свойства
Важнейшей из характеристик углеволокна остается его исключительная тепловая стойкость. Даже если вещество прогрето до 1600 — 2000 градусов, то при отсутствии кислорода в окружающей среде его параметры не поменяются. Плотность этого материала, наряду с обычной, бывает и линейной (измеряется в так называемых тексах). При линейной плотности 600 tex масса 1 км полотна будет составлять 600 г
Критически важное значение во многих случаях имеет и модуль упругости материала, или, как говорят иначе, модуль Юнга
У высокопрочного волокна этот показатель составляет от 200 до 250 ГПа. Высокомодульное углеволокно, сделанное на базе ПАН, имеет модуль упругости примерно 400 ГПа. У жидкокристаллических решений этот параметр может варьироваться от 400 до 700 ГПа. Модуль упругости вычисляют, отталкиваясь от оценки его величины при растягивании отдельных графитовых кристаллов. Ориентировку атомных плоскостей устанавливают с использованием рентгеноструктурного анализа.
По умолчанию поверхностное натяжение составляет 0,86 Н/м. При обработке материала для получения металлокомпозитного волокна этот показатель вырастает до 1,0 Н/м. Определять соответствующий параметр помогает измерение по способу капиллярного подъема. Температура плавления волокон на базе нефтяных пеков равна 200 градусам. Прядение происходит примерно при 250 градусах; температура плавления других видов волокон прямо зависит от их состава.
Максимальная ширина углеродных полотен зависит от технологических требований и нюансов. У многих производителей она составляет 100 или 125 см. Что касается осевой прочности, то она будет равна:
- у высокопрочных изделий на базе ПАН от 3000 до 3500 МПа;
- у волокон со значительным удлинением строго 4500 МПа;
- у высокомодульного материала от 2000 до 4500 МПа.
Теоретические расчеты устойчивости кристалла при растягивающем усилии в сторону атомной плоскости решетки дают оценочную величину 180 ГПа. Ожидаемый предельный практический показатель равен 100 ГПа. Но в экспериментах пока не подтверждено наличие уровня более 20 ГПа. Реальная прочность углеволокна лимитируется его механическими дефектами и нюансами производственного процесса. Установленная в исследованиях на практике прочность к растяжению участка длиной 1/10 мм составит от 9 до 10 ГПа.
Отдельного внимания заслуживает карбоновое волокно T30. Этот материал применяется в основном в получении удилищ. Такое решение отличается легкостью и отличным балансом. Индекс Т30 обозначает модуль упругости 30 тонн.
Достоинства карбоновых рам
Карбон имеет очень высокую прочность, превосходя в этом некоторые высокопрочные стали. И в тоже время – очень малый вес, в 2-3 раза меньший, чем у титана. По комплексному параметру «прочность-легкость» углепластик – один из лучших, если вообще не самый лучший материал. Именно эти качества обеспечили его использование при изготовлении не только велосипедов, но и многих других бытовых и промышленных изделий высшего качества и даже в авиастроении.
Велосипедные рамы из карбона получаются прочными и очень легкими. Вдобавок к этому углепластик хорошо гасит вибрацию и не поддается коррозии. По сравнению с титаном, он обеспечивает большую жесткость рамы, облегчая езду по пересеченной местности и в гору. Усовершенствованная технология производства карбоновых деталей позволяет изготавливать не только рамы для велосипедов, но и другие элементы – выносы, рули, вилки, шатуны, подседельные штыри и даже звездочки.
Производство из материала 21-го века по технологиям 19-го
Нужно сказать, что процесс изготовления карбоновой рамы мало похож на производство 21 века. Скорее он напоминает работу в мастерской дофордовских времен. Основная часть операций делается вручную. Это объясняет, конечно, дороговизну карбона, из-за которой невозможен массовый спрос. А без массового спроса нет экономического смысла разрабатывать и строить автоматические линии. Процесс изготовления велосипедных рам из углепластика требует много рабочих рук. Это наряду с дороговизной материала делает карбоновые рамы дорогим удовольствием.
Итак, что представляет собой процесс изготовления велосипедной рамы из углепластика?
Из всех компаний-производителей велосипедов лишь две (Giant и Time) в качестве исходного сырья использует карбоновые нити. Другие фирмы предпочитают закупать уже готовую углеволоконную ткань.
Если рассматривать процесс изготовления рам на примере Giant и Time, то исходный материал для карбоновых велосипедных рам представляет собой катушку толстых ниток. Вернее сказать, несколько десятков катушек, которые надеты на бобины. Множество карбоновых нитей проходят через станок, превращаясь в листы, шириной в 3 фута, пропитанные смолой.
Преимущества углеродного волокна
Можно с уверенностью сказать, что не совсем дорогие композиты из углеродных волокон, будут способны внести большой вклад для различных видов технологий, в том числе для технологий, который только начинают развиваться и также не стоит забывать особое значение этого волокна в человеческой жизни. При изготовлении автомобилей, автобусов, поездов, самолетов, кораблей и т.д, начинают появляться панели и конструкции с довольно легким весом, что постепенно может привести к экономии и всемирному уменьшению употребления энергии. Недорогое углеродного волокна является национальной целью, к реализации ряда технологических прорывов производства.
Производство углеродных волокон
Углеродное волокно — это супер прочный материал, и в то же время очень легкий. Углеродные волокна характеризуются высокой силой натяжения, низкимудельным весом, низким коэффициентом температурного расширения и химической инертностью. Поэтому углеродное волокно часто используют в сфере аэронавтики, изготовления спортивного инвентаря, автомобилей, при строительстве и, конечно же, в музыкальных инструментах.Углеродные волокна, обычно, получают термической обработкой химических или природных органических волокон, при которой в материале волокна остаются главным образом атомы углерода. Первый из них представляет собой окисление исходного волокна на воздухе при температуре 250 °C. После окисления следует стадия карбонизации — нагрева волокна в среде азота или аргона при температурах от 800 до 1500 °C. В результате чего происходит образование графитоподобных структур.Процесс термической обработки заканчивается графитизацией при температуре 1600—3000 °C, которая также проходит в инертной среде. Свойства полученных углерод / графитовых волокон, могут повлиять на большое количество факторов, таких как: кристалличность, движение молекул, состав углерода и присутствие дефектов. Полученные в результате углеродные волокна обрабатываются с целью улучшения их свойств и характеристик.
2016, Aquamir.UA
При использовании материала, обратная активная гиперссылка обязательна. Спасибо.
Метки: карбон, Обзоры, углеводородное волокно
Углеродное волокно как материал основа для производства композиционных материалов
Углеродное волокно – материал, состоящий из тонких нитей диаметром от 3 до 15 микрон, образованных преимущественно атомами углерода. Атомы углерода объединены в микроскопические кристаллы, выровненные параллельно друг другу. Выравнивание кристаллов придает волокну большую прочность на растяжение и пр. свойства.
Углеродное волокно является основой для производства углепластиков (или карбона, карбонопластиков, от “carbon”, “carbone” – углерод). Углепластики – полимерные композиционные материалы из переплетенных нитей углеродного волокна, расположенных в матрице из полимерных (чаще эпоксидных) смол.
На основе углеродного волокна производят:
– композитную (углеродную) арматуру. Углеродная арматура представляет собой материал, который состоит из основы в виде углеродного волокна и связующего: термореактивной синтетической смолы. Углеродная арматура изготовляется методом пултрузии — протяжкой пропитанных связующим армирующих волокон через нагретую формообразующую фильеру;
– двунаправленные ткани: комбинированную (углеродную и арамидную) ткани, стеклоткань саржевого или полотняного переплетения, углеродную ткань саржевого или полотняного плетения, углеродную ткань-сатин;
– дизайнерские ткани;
– мультиаксиальные ткани: биаксильные ткани, квадроаксильные ткани,
– углеродное нетканое полотно. Нити углеродного волокна в однонаправленных нетканых материалах располагаются строго параллельно друг другу. Нити фиксируются стеклянной сеткой и/или эпоксидным биндером;
– однонаправленные углеродные ленты. Однонаправленные углеродные ленты – это текстиль, где свыше 75% волокон расположены в одном направлении. В качестве утка используется стекловолокно или арамидное волокно;
– препреги. Препреги — композиционные материалы-полуфабрикаты. Их получают путем пропитки армирующей волокнистой основы равномерно распределенными полимерными связующими. Пропитка осуществляется таким образом, чтобы максимально реализовать физико-механические свойства армирующего материала. Методы с использованием пропитки волокна позволяют на 30% улучшить свойства материала;
– системы внешнего армирования;
– преформу-рукав;
– фибру. Фибра – нарезанное углеродное волокно. Используется в качестве усиливающей добавки в бетон, асфальтобетон;
– прочие материалы: жгуты, углерод-углеродные композиционные материалы, фибры и т.д.
Виды волокон карбона. Полотно
Волокна могут быть короткими, резаными, их называют «штапелированными», а могут быть непрерывные нити на бобинах. Это могут быть жгуты, пряжа, ровинг, которые затем используются для изготовления тканого и нетканого полотна и лент. Иногда волокна укладываются в полимерную матрицу без переплетения (UD).
Так как волокна отлично работают на растяжение, но плохо на изгиб и сжатие, то идеальным вариантом использования углеволокна является применение его в виде полотна Carbon Fabric. Оно получается различными видами плетения: елочкой, рогожкой и пр., имеющими международные названия Plain, Twill, Satin. Иногда волокна просто перехвачены поперек крупными стежками до заливки смолой. Правильный выбор полотна по техническим характеристикам волокна и виду плетения очень важен для получения качественного карбона.
В качестве несущей основы чаще всего используются эпоксидные смолы, в которых полотно укладывается послойно, со сменой направления плетения, для равномерного распределения механических свойств ориентированных волокон. Чаще всего в 1 мм толщины листа содержится 3-4 слоя .
3.Связующие
В качестве матриц (связующих) при изготовлении судовых конструкций используются преимущественно эпоксидные н полиэфирные синтетические смолы .
Эпоксидные смолы используются двух типов: термопласты и реактопласты. Термопласты все еще находятся в стадии разработки из-за их высокой стоимости. Чаще всего используют смолы реактопласты, которыми пропитывают углеродистые волокна, а после подвергают нагреванию. Процесс, когда волокно и смолу соединяют в матрице, называют полимеризацией .
До момента отверждения связующее остается вязкотекучей жидкостью. В определенных условиях (при повышении температуры, добавлении иницирующих реакцию веществ и т. п.) молекулы этой жидкости взаимодействуют между собой, образуя большие пространственные молекулы, вследствие чего вся масса связующего необратимо отверждается — затвердевает.
Сравнительно новым классом термостойких высокомолекулярных соединений являются полиамидные смолы. Их главное отличие от полиэфирных и эпоксидных смол заключается в более высоких механических характеристиках и большей стойкости к окислению при высоких температурах (после отверждения). Однако применение полиамидных смол требует разработки специальной технологии нзготовлення ПКМ. Основные характеристики перечисленных смол приведены в табл. 1 .
Сборка рамы
Рама велосипеда представляет собой замкнутую конструкцию со сложной поверхностью, которая в разных местах имеет различную конфигурацию – в виде цилиндра, тора, или иных криволинейных поверхностей. Для удобства сборки рама подразделяется на отдельные элементы, которые формируются путем наложения листовых заготовок на шаблоны (матрицы), форма которых идентична элементам рамы. Эта работа напоминает изготовление деталей из стеклопластика. Те, кому приходилось делать из него обвесы для своего мотоцикла или машины, смогут сделать это и из карбона.
Листовая заготовка разрезается на фрагменты различной конфигурации и размеров – в зависимости от того, для какой части рамы она предназначена. Причем при нарезании частей учитывается не только конфигурация заготовки, но и расположение нитей в ней. Нарезанные фрагменты раскладываются по коробкам, из которых рабочие подбирают себе куски необходимых размеров.
На сборочных столах имеются ячейки (гнезда), в которых лежат карбоновые фрагменты для определенных деталей. Перед наложением листовых заготовок на матрицу, они разогреваются на подогретой пластине. Матрицу тоже подогревают для придания углепластику эластичности и гибкости. Каждая деталь рамы требует наложения нескольких слоев заготовок. Наиболее простым является изготовление трубчатых частей рамы. Листовой фрагмент просто несколько раз оборачивается вокруг шаблона в виде трубки.
Наиболее сложные в изготовлении – зона каретка и рулевой колонки.
После того как все части рамы сформованы, их укладывают в пластмассовую форму. Во внутреннюю полость рамы вводят эластичной баллон из полиуретана и подкачивают его – чтобы он создавал давление на стенки рамы изнутри. В отверстие каретки и во втулку руля вставляют стальные сердечники. Отрезают излишки карбонового волокна и отправляют подготовленную раму в холодильник, где она ожидает своей очереди на формовку и обжиг в печи.
Формовка
Для горячего формования раму укладывают в форму. Ввиду сложности конфигурации изделия, форма состоит из различных подвижных частей, которые пододвигаются в нужное положение к раме и фиксируются болтами. Когда все части нижней половины формы находятся на своих местах и зафиксированы, опускается с помощью гидравлики верхняя часть формы. В результате рама оказывается замкнутой со всех сторон.
Затем матрица с рамой отправляется в печь на температурную формовку (обжиг). Благодаря давлению находящегося во внутренней полости рамы полиуретанового баллона, наружная поверхность рамы в точности повторяет конфигурацию формы. Перекрывающие друг друга карбоновые листы сплавляются композитной смолой, образуя монолитную бесшовную поверхность. Излишки углепластикового композита выдавливаются из матрицы.
Финишная обработка
После охлаждения форма разбирается, и извлекается готовая рама. Впрочем, говорить – «готовая» – еще рано. Ей предстоит финишная обработка – зачистка напильником и рашпилем, шлифовка, полировка и прочее. Во время зачистки и полировки образуется много карбоновой пыли, которая повисает в воздухе. Чтобы избежать ее вдыхания, люди работают в защитных костюмах и масках. Вентиляторы направляют пыльный воздух к стенам, по которым струится вода, смывающая карбоновую пыль.
Заключительной операцией является тестирование. На раму с определенной высоты бросают груз и измеряют сопротивление удару. Тест показывает, насколько готовое изделие соответствует необходимым требованиям.
И в завершении небольшое видео о производстве карбоновых рам на заводе Giant:
https://youtube.com/watch?v=EsZnY2gdK6Y
Что собой представляют карбоновые спиннинги
Карбоновые спиннинги изготовлены из композитного материала, который состоит из углеродных нитей, находящихся в оболочке из смол. Эти нити обладают высокой прочностью. Для изготовления удилища из карбона применяют ткань из углеродных нитей, находящихся под некоторым углом друг к другу. Эта ткань обладает высокой жесткостью и легкостью.
Параметры спиннингов из углепластика различаются в зависимости от модульности графита и особенностей изготовления. В состав материала производители добавляют смолы, от качества которых зависит чувствительность, строй удилищ. Так, удочки с быстрым строем содержат меньшее количество смол, а спиннинги с медленным строем — большее их число.
Ручное ламинирование
Самый простой и самый старый метод в процессе штамповки. Технологический процесс называется ручным ламинированием. Поскольку должны быть соблюдены только минимальные технические требования, эта технология подходит для небольших серий и очень простых компонентов. Но как эта техника работает сейчас? При ручном ламинировании каждое волокно вручную пропитывается смолой с помощью кисти или валика. Затем следует модификация, а именно — шлифовка, покраска прозрачным лаком или аналогичные дополнительные шаги.
С другой стороны, эту технику трудно превзойти по возможности создания сверхлегких деталей.
Классификация и виды углеродных волокон
Если ориентироваться на прочность и конечную температуру термообработки, углеродные волокна могут быть разделены на следующие категории:
На основе свойств углеродные волокна могут быть сгруппированы в:Сверхпрочное волокно, типа UHM (коэффициент >450Гпа)Прочное волокно, типа HM (коэффициент между 350—450Гпа)Волокно средней прочности, типа IM (коэффициент между 200—350Гпа)Прочное на разрыв волокно, типа HT (модуль<100Гпа прочность на разрыв> 3.0Гпa)Волокно с высокой прочностью ( коэффициент растяжения> 4.5 Гпа)
На основе волоконных материалов, углеродные волокна подразделяются на:
Углеродные волокна на основе полиакрилонитрилаУглеродное волокно из каменноугольных и нефтяных пековУглеродные волокна на основе мезофазыНа основе вискозных штапельных волоконУглеродные волокна с добавлением вискозного шелкаАктивированные сорбирующие ткани
На основе температуры термообработки, углеродные волокна, подразделяются на:
Тип—1, используются при высокой термической обработки (НТТ), где необхожимая температура— 2000 ° C.Тип—2, эти углеродные волокна поддаются средней термообработки (IHT), где температура термообработки должна быть около или чуть выше 1500 ° C.Тип—3, данный тип углеродных волокон используется при низкой термообработки, где температура не превышает 1000° C.
Удилища из карбона
Карбон (он же углепластик) является, пожалуй, лучшим материалом для удилища, особенно спиннингового.
Углепластиковые удилища характеризуются отличной чувствительностью при сохранении высоких показателей прочности; также они обладают меньшим весом по сравнению с моделями из стекловолокна.
Каждое карбоновое удилище имеет определенный модуль содержания графита, который обозначается на бланке (М1, М2 и т.п.).
Чем выше уровень содержания графита, тем большей жесткостью и скоростью реакции обладает удилище, тем более дальним будет заброс.
Однако вместе с этим повышается и хрупкость удилища. Какой модели отдать предпочтение – выбор сугубо индивидуальный.
Выбираем карбоновое удилище
Карбоновый спиннинг нужно выбирать по таким характеристикам:
- Вес. Различают изделия ультралегкие — весом до 7 г, легкого класса — весом 7−15 г, средние — весом 15−40 г, тяжелые — более 40 г.
- Строй. Спиннинги могут быть: быстрого строя, когда изгибается только конец бланка; медленного строя, когда изгибается весь бланк, начиная от ручки.
- Длина. Удилища м.б. размером от 180 до 360 см.
- Тест, который является условным весом приманки и составляет от 1 до 20 г.
https://youtube.com/watch?v=On_FF4ORIpU
Поплавочное
Карбоновые поплавочные спиннинги бывают:
- с глухой оснасткой;
- маховые;
- матчевые;
- английские удилища;
- штекерные.
Удилищем с глухой оснасткой можно ловить рыбу в сложных условиях, например в заросшем пруду. Здесь нельзя применять изделие с катушкой, т.к. леска будет цепляться за траву. Длина такой снасти должна быть меньше нависающих над прудом ветвей, строй должен соответствовать размеру трофея.
Маховое удилище также не оснащается катушкой. Эта снасть обладает мягким строем. Таким спиннингом пользуются на открытых участках реки. Снасть позволяет с легкостью забрасывать приманку в одно и то же место. Английская удочка оснащается катушкой и применяется для проводной ловли на течении. Конструкция не должна быть слишком гибкой.
Производство
Углепластик
Прессование. Углеткань выстилается в форму, предварительно смазанную антиадгезивом (например, мыло, воск, воск в бензине, Циатим-221, кремнийорганические смазки). Пропитывается смолой. Излишки смолы удаляются в вакууме (вакуум-формование) или под давлением. Смола полимеризуется, иногда при нагревании. После полимеризации смолы изделие готово.
- Контактное формование. На примере изготовления бампера: берётся металлический исходный бампер, смазывается разделительным слоем. Затем на него напыляется монтажная пена (гипс, алебастр). После отвердевания снимается. Это матрица. Затем её смазывают разделительным слоем и выкладывают ткань. Ткань может быть предварительно пропитанной, а может пропитываться кистью или поливом непосредственно в матрице. Затем ткань прокатывается валиками — для уплотнения и удаления пузырьков воздуха. Затем полимеризация (если отвердитель горячего отверждения, то в печи, если нет, то при комнатной температуре — 25 °C). Затем бампер снимается, если надо — шлифуется и красится.
- Вакуумная инфузия. На подготовленную матрицу выкладывается углеродная ткань (без пропитки), далее выкладываются технологические слои для равномерного распространения связующего. Под технологический пакет подаётся разрежение. После этого открывается клапан подачи связующего и оно, под действием вакуума заполняет пустоты и пропитывает углеродную ткань.
- Вакуумное формование. Это изменение формы плоских заготовок (листов или плёнок) из термопластичного полимерного материала при повышенных температурах и воздействии вакуума в объёмные формованные изделия. За счёт относительно невысокой стоимости технологической оснастки, данная технология оказывается крайне привлекательной при изготовлении партий изделий от 10 до 5000 шт., а иногда и до 30.000 шт.
- Пултрузия. Технология изготовления высоконаполненных волокном композиционных деталей с постоянной поперечной структурой. В настоящее время активно используется в производстве полимерных композиционных материалов, например, для производства углеродных ламелей (пластин).
- Намотка. Суть технологии заключается в непрерывном наматывании предварительно пропитанного ровинга/ов (стеклянного, углеродного, базальтового, комбинированного) или ленты на предварительно подготовленную форму – мандрель. После намотки необходимого количества слоёв, мандрель с намотанными слоями помещается в нагревательную печь для дальнейшей полимеризации.
- RTM. Сухой армирующий материал укладывается между двух частей герметично закрытой жёсткой оснастки. Связующее низкой вязкости подаётся под давлением в пресс-форму, вытесняя воздух в сторону дренажных каналов до тех пор, пока форма не будет полностью заполнена. Пресс-формы для этой технологии, как правило, изготавливаются из металла с низким КЛТР. Данная технология хорошо подходит для мелкосерийного и серий средних объёмов от 500 до 2 0000 изделий в год.
- LFI. Технология LFI (Long Fiber Injection — длинноволоконная инжекция) была разработана немецкой фирмой Krauss Maffei в 1995 году. Характеристика производства: инжекция длинного волокна, процесс используемый для производства компонентов интерьера и экстерьера автомобилей, конструкция которых имеет сложную форму, крупные габариты и окрашенную поверхность класса А. В этом процессе рубленое волокно из ассемблированного ровинга, напыляется в форму (матрицу) с контролируемой температурой. В это же время смешивается жидкий изоцианат и полиол, подаётся совместно с рубленым волокном в матрицу. Все эти компоненты напыляются в форму (матрицу), форма смыкается и заполняются путём расширения полиуретановой пены в результате химической реакции введённых компонентов. Несколько минут спустя, полимеризация закончена и изделие может быть извлечено из матрицы.
- SMC/BMC. Материал нарезается, в соответствии со схемой раскроя, и переносится в пресс-форму, нагретую до рабочей температуры. Пресс-форма смыкается, в результате чего под давлением материал растекается в полости формы и отверждается. В конце цикла изделие извлекается из пресс-формы, и производится его окончательная механическая обработка и окраска (если это необходимо).
Трубы и иные цилиндрические изделия производят намоткой. Форма волокна: нить, лента, ткань. Смола: эпоксидная или полиэфирная. Возможно изготовление форм из углепластика в домашних условиях, при наличии опыта и оборудования.
углепластиковая подставка под кофе.
Достоинства и недостатки материала
Спиннинг, изготовленный из карбона, обладает всеми показателями качества данного материала.
Преимуществами карбоновых удилищ являются:
- легкость;
- повышенная чувствительность;
- высокая эффективность.
Рыболов, который применяет карбоновый спиннинг, чувствует даже небольшое движение приманки и может определить осторожную поклевку. Спиннинг отличается высокой упругостью и сбалансированностью, что позволяет осуществлять дальний заброс лески и выдерживать сопротивление крупной рыбы.
Недостатками карбоновых удочек являются:
- хрупкость;
- высокая стоимость;
- необходимость использования кофров для перевозки спиннинга.
Часто рыбаку приходится сравнивать стекловолокно, стеклопластик, фибергласс — что лучше для спиннинга. Опытные рыболовы выбирают из материалов наилучший — композит из углеродных нитей, карбон.
Таким образом, можно сделать вывод, что при должном уходе углепластиковые удочки являются удобными, надежными и долговечными. В конце рыбалки надо очищать удилища от загрязнений, что продлит срок их эксплуатации.
Наиболее популярны карбоновые спиннинги штекерного вида. Они лучше телескопических по всем характеристикам. Поскольку телескопические карбоновые удочки состоят из нескольких колен, каждое звено увеличивает вес и уменьшает чувствительность снасти.
Единственным достоинством телескопической удочки является ее компактность в сложенном виде, что удобно при перевозке. Тем не менее телескопическое удилище из карбона намного легче и чувствительнее телескопических удочек, изготовленных из прочих материалов.
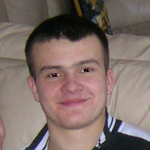
Эта тема закрыта для публикации ответов.