Химический состав
Сплав D2 разработан на основе высокоуглеродистой стали. Содержание углерода в его составе — 1,4-1,6%. Его высокая концентрация способствует образованию большого количества карбида железа. Особую прочность и износоустойчивость ему придают тугоплавкие металлы, концентрация которых составляет:
- молибдена – 0,8-1,2%;
- вольфрама – 0,9-1,1%.
Они вводятся в расплавленный металл в порошковом виде и замещают железо в соединениях с углеродом. Образуются прочные карбиды вольфрама и молибдена, придающие металлу свойства:
- высокой прочности при нагреве;
- способности к закаливанию;
- равномерного распределения возникающих в процессе закалки внутренних напряжений;
- предотвращения хрупкости.
Повышает антикоррозионные характеристики стали Д2 добавление хрома, в количестве более 11%. Дополнительную прочность придают сплаву карбиды хрома, образующиеся в процессе взаимодействия элементов.
Кремний и марганец добавляются в равных долях, по 0,6%, и обеспечивают стабилизирующее и упрочняющее влияние на внутреннюю структуру сплава.
Известно, что сера и фосфор способствуют ухудшению механических свойств, снижают износоустойчивость, одновременно повышая хрупкость металла. Содержание этих элементов снижено до тех пределов, когда их вредное воздействие не отражается на качестве стали:
- сера – 0,03%;
- фосфор – 0,04%.
Преимущества и недостатки метода
Каждый метод вычисления твердости поверхности обладает своими определенными достоинствами и недостатками. Принято считать, что испытание на твердость по Роквеллу и Бринеллю являются основными, так как позволяют получить наиболее точный результат.
К достоинствам метода измерения твердости по Роквеллу HRC можно отнести нижеприведенные моменты:
- Технология определяет возможность тестирования поверхностей с повышенной твердостью.
- При тестировании поверхность повреждается несущественно, что позволяет исследовать уже готовые изделия.
- Существенно упрощается процесс расчетов показателя твердости, так как нет необходимости в замере диаметра получаемого отпечатка после снятия прилагаемой нагрузки.
- На проведение измерений по Роквеллу уходит всего несколько секунд.
Читать также: Паяльник для полипропиленовых труб как пользоваться видео
https://youtube.com/watch?v=ZBPiLnaaXvE
Однако есть и несколько существенных недостатков, которые также нужно учитывать:
- В сравнении с методом по Бринеллю, получаемый результат не так точен.
- Для повышения точности проводимых измерений следует тщательно подготовить поверхность.
Несмотря на то, что получаемые результаты могут иметь достаточно высокую погрешность, этот метод получил широкое распространение в машиностроительной и других отраслях промышленности, так как на тестирование уходит мало времени.
Показатель твердости зависит от достаточно большого количества моментов, к примеру, химического состава. Кроме этого, металлы могут улучшаться закалкой и другими видами термической обработки. Сегодня можно встретить довольно много методической литературы с таблицами, в которых указывается твердость для распространенных материалов. Принимаются эти значения зачастую при выполнении расчетов или проектировании.
На точность проводимых измерений может оказывать влияние:
- Толщина испытуемого образца. Согласно принятым нормам при проникновении алмазного наконечника на 0,2 мм толщина испытуемого образца должна быть не меньше 2 см. В противном случае, полученные данные будут считаться искаженными.
- Если один образец применяется для проведения нескольких тестов, то расстояние между отпечатками должно быть не менее трех их диаметров. Соблюдение этого правила также позволяет получить более точные результаты.
- Результаты на циферблате могут отличаться в зависимости от положения исследователя. Повторные тестирования должны проводиться с одной точки обзора, иначе полученные результаты могут отличаться.
https://youtube.com/watch?v=tJsDHGPNuG0
В заключение отметим, что сегодня подобные исследования проводятся все реже. Это связано с тем, что при изготовлении заготовок достигают высокой точности химического состава и физико-механических свойств. Поэтому каждой марке металла соответствует определенный показатель твердости по Роквеллу. Измерения зачастую проводятся после выполнения химико-термической обработки, когда от соблюдения применяемой технологии зависит конечный результат.
Если вы нашли ошибку, пожалуйста, выделите фрагмент текста и нажмите Ctrl+Enter.
Методика проведения испытания промышленным твердомером Роквелла
Метод Роквелла.
- Выбрать подходящую для проверяемого материала шкалу (А, В или С).
- Установить соответствующий индентор и нагрузку.
- Перед тем, окончательным измерение надо сделать два пробных, неучитываемых отпечатка, чтобы проверить правильность установки индентора и стола.
- Установить эталонный блок на столик прибора.
- Приложить предварительную нагрузку в 10 кгс, обнулить шкалу.
- Приложить основную нагрузку и дождаться достижения максимального усилия.
- Снять нагрузку.
- Прочесть на циферблате по соответствующей шкале значение твёрдости (цифровой прибор показывает на экране значение твёрдости).
- Порядок действий при проверке твёрдости испытуемого образца такой же, как и на эталонном блоке. Допускается делать по одному измерению на образце при проверке массовой продукции.
О правильном использовании
Не пользуйтесь разделочными досками из камня, стекла. Оптимальный вариант – дерево и бамбук, а также прочный пластик. Даже самые крепкие клинки со временем затупятся о стеклянную доску. Также из-за скользкого материала нож может легко отскочить, что приведет к травме.
Не подвергайте нож перегреванию. Если нужно резать горячие продукты, то ненадолго нужно поместить нож в морозилку. Чтобы аккуратно нарезать сыр, замороженное мясо или сливочное масло нужно – согреть нож в горячей воде.
Чтобы облегчить нарезку лука, лезвие стоит погрузить в посуду с холодной водой на несколько секунд.
Лезвия из углеродистой стали нельзя мыть в горячей воде.
После мытья тщательно вытирайте, не оставляйте нож надолго в воде.
Для всех типов ножей предпочтительна ручная мойка – в этом случае они дольше сохранят свои эксплуатационные свойства.
Следует применять ножи только по назначению. Это продлит срок службы и убережет вас от травм. Для специфических операций приобретите кухонные ножницы, канцелярский нож.
Как измеряется твердость по шкале Роквелла?
Шкала Роквелла измеряет относительную твердость металла. Она основана на том, насколько глубокой является полученная вмятина при ударе тяжелого предмета. Так как же проводят испытания металла?
Во-первых, металл должен быть термически обработан и абсолютно плоским. Иначе результаты теста будут неточными.
Одним из методов является использование конуса с алмазным наконечником для принудительного удара по металлу. Затем тестеры измеряют, насколько глубоко конус проник в поверхность. Затем, это измерение преобразуется в шкалу, которая показывает различные металлы, которые были испытаны, и как они все связаны друг с другом.
Одним из небольших недостатков при испытании клинка ножа является то, что оно оставляет небольшую точечную вмятину на поверхности, что некоторые могут счесть дефектом. Знак испытания может быть скрыт, если испытание проводится в области, которая находится под рукояткой.
Тест Роквелла фактически состоит из двух тестов. Во время первого испытания создается лишь незначительное усилие, используя алмазный наконечник, похожий на карандаш в сверлильном станке. Это гарантирует, что зона испытания абсолютно плоская и является мишенью для основного испытания на давление. После того, как сделано первое измерение, тест повторяется в той же точке. Давление резко возрастает для этого второго теста, при этом приблизительно 150 кг. давления находятся на этом алмазном наконечнике.
Разница между давлением, использованным для первого и второго испытания, представляет собой число твердости по шкале Роквелла. Два (или более) испытания одного и того же куска металла дадут среднее значение для данного конкретного куска стали.
Способы перехода между шкалами
Определив диаметр отпечатка с помощью специального оборудования, можно с помощью таблиц определить твердость. Таблица твердости металлов – проверенный помощник в вычислении данного механического параметра. Так, если известно значение по Бринеллю, можно легко определить соответствующее число Виккерса или Роквелла.
Нож на заказ
На большинство продукции в нашем магазине возможно нанесение инициалов, надписей, логотипов, фирменной символики.
Личный Кабинет
Осуществляется доставка по всем регионам Российской Федерации: Московская область, Самара, Челябинская область, Свердловская область (Екатеринбург), Уфа (Республика Башкортостан), Республика Татарстан, Курганская область, Тюменская область, Пермский край, Оренбургская область, Краснодарский край, Удмуртская Республика и далее – все регионы России. Наши менеджеры будут рады предоставить вам всю необходимую информацию.
Вся информация на сайте носит справочный характер и не является публичной офертой, определяемой положениями Статьи 437 Гражданского кодекса Российской Федерации. Технические параметры (спецификация) и комплект поставки товара могут быть изменены производителем.
Источник
Аналоги сплава и его применение
Марка стали D2 была разработана в 60-е годы прошлого века в Соединенных Штатах и первоначально использовалась для нужд промышленности. Из сплава изготавливали высокоскоростные резцы по металлу, которые могли работать при высоких температурах. Сегодня эта марка популярна во всем мире и имеет множество аналогов:
- Х155CrMo12 – в Германии;
- SLD – Японии;
- 1,2379 – в Евросоюзе;
- SKD-11 – Швеции.
В России заменителем стали D2 является марка Х12МФ, состав которой регламентируется ГОСТом 5950. Ее сортамент представлен:
- различными видами проката;
- калиброванным прутком и серебрянкой;
- полосой и коваными заготовками.
Инструментальная сталь D2, как и ее аналоги, нашла широкое применение:
- в машиностроительной отрасли;
- производстве металлообрабатывающих инструментов;
- бритвенных лезвий.
Особенно востребована она в качестве материала для изготовления элитных ножей, что связано с ее способностью в течение длительного времени держать хорошую заточку. Ее в норме должно хватать на разделку крупной туши. Из сплава получают широкий ассортимент ножей:
- универсальных складных, включая и подарочные варианты;
- шейных охотничьих ножей, предназначенных для свежевания добычи;
- туристических, имеющих широкий спектр применения;
- разделочных, для разрезания больших туш.
Заточка лезвия
У мировых производителей есть три вида заточки.
«Универсальная» – наиболее привычная для славян. В таком случае клинок наточен с обеих сторон.
«Под правую руку» – имеет одну правую заточенную сторону, рассчитана для правшей.
«Под левую руку» – сделана аналогичным образом для левшей. Чаще всего односторонняя заточка встречается у японских производителей.
Новинка обработки лезвий – «лазерная заточка». Лазером закаливают клинок. В результате на лезвии чередуются обработанные твердые участки и необработанные мягкие. Потому на клинке видны небольшие вертикальные полоски. Благодаря им нож является самозатачивающимся.
Любой стальной нож можно точить в домашних условиях при помощи точильного камня или станка. Керамические же рекомендуют отдавать специалистам или часто менять, если купленный нож имеет низкую стоимость.
Показатель твердости стали
Самый высокий показатель HRC не обязательно является лучшим.
Более твердая сталь, как правило, лучше держит кромку, чем более мягкая сталь, но она также с большей вероятностью трескается или выходит из строя. На самом деле, если она действительно твердая, она может разбиться, как стекло на бетоне!
Сталь, используемая при изготовлении ножа, также имеет большое отношение к тому, насколько хорошо нож будет удерживать кромку. Каждый отдельный стальной сплав имеет свой оптимальный диапазон, который уравновешивает твердость с производительностью и предназначением.
Так почему же показатель ножа по Роквеллу имеет значение? Что такое хорошая твердость по Роквеллу для ножа?
Твердость ножа очень важна с точки зрения его производительности и долговечности. Например, более твердая сталь с RC 58-62 будет держать кромку лучше, чем более мягкая сталь. Однако, эта же самая твердая сталь менее прочна и более склонна к растрескиванию или даже поломке
Некоторые кухонные ножи с высокой твердостью требуют особой осторожности, чтобы не повредить тонкую режущую кромку
Более мягкая сталь более долговечна за счет свой высокой упругости. В большинстве топоров и зубил используется более мягкая сталь, которая выдерживает удары, с которыми они сталкиваются в повседневной работе.
Поскольку карманные ножи и охотничьи ножи обычно не используются для строгания и рубки древесины, они выигрывают от использования более прочной стали, которая сохраняет отличную остроту для нарезки мягких материалов.
Однако, нож для выживания, к которому вы собираетесь приложить экстремальные усилия, только выиграет от твердости по Роквелу 55-58. Нож, который мог бы резать кости и твердую древесину, в первую очередь, должен быть прочным. Нож с более низкой твердостью может затупиться быстрее, но с большей вероятностью переживет большое количество ударов и механических повреждений.
Испытание по Роквеллу помогает производителям ножей уравновешивать три наиболее важных фактора, которые могут повлиять на качество их готовой продукции: твердость, гибкость и вязкость. Наличие этих трех факторов в правильном балансе позволяет им производить ножи для различных сфер использования.
Существует несколько различных аббревиатур, которые могут использоваться изготовителем ножей при указании твердости: HR, HRc, HR C, RC, Rc, C по шкале Роквелла, шкала твердости Роквелла C. Независимо от того, как написано о ножевой стали, все они ссылаются на одну и ту же шкалу С. Это может немного запутать, но просто знайте, что рейтинги сами по себе одинаковы – какое бы обозначение не использовал производитель.
Стэнли П. Роквелл был металлургом на заводе по производству шарикоподшипников в Новой Англии в 1919 году. Он разработал шкалу твердости для того, чтобы измерять твердость шариков для подшипников быстро, точно и с высокой повторяемостью.
Производители всего, начиная от пружин для часов и заканчивая колесами для поездов, давно нуждались в таком испытании и быстро применяли шкалу Роквелла для всех видов стали, а также других металлов, деталей. В конце концов, тест был адаптирован даже для испытаний неметаллических материалов – даже пластмасс.
Стандарты
- Международный ( ISO )
- ISO 6508-1: Металлические материалы — испытание на твердость по Роквеллу — Часть 1: Метод испытания (шкалы A, B, C, D, E, F, G, H, K, N, T)
- ISO 6508-2: Металлические материалы. Испытание на твердость по Роквеллу. Часть 2: Проверка и калибровка испытательных машин и инденторов.
- ISO 6508-3: Металлические материалы. Испытание на твердость по Роквеллу. Часть 3: Калибровка эталонных образцов.
- ISO 2039-2: Пластмассы. Определение твердости. Часть 2: Твердость по Роквеллу.
- Стандарт США ( ASTM International
ASTM E18: Стандартные методы определения твердости по Роквеллу и поверхностной твердости по Роквеллу металлических материалов
)
Технические особенности стали марки D2
Есть пять характеристик для оценки сплава:
- Твердость. Обладает высоким показателем – до 64 HRC по Роквеллу.
- Жесткость. Отличается прочностью, но является недостаточно жестким, что приводит к неудобствам при заточке изделий.
- Износоустойчивость к абразивному воздействию. Благодаря твердости этот показатель у сплава высокий.
- Коррозионная стойкость. Данный вид стали не относится к нержавеющим, поскольку не содержит достаточного количества хрома, но сопротивляется ржавчине. Устойчивость к коррозии оценивается как средняя.
- Защита краев от завалов. При эксплуатации лезвие изделия из D2 способно долгое время сохранять свою остроту.
Измерение микротвердости
Метод измерения микротвердости регламентирован ГОСТ 9450. Определение микротвердости (твердости в микроскопически малых объемах) проводят при исследовании отдельных структурных составляющих сплавов, тонких покрытий, а также при измерении твердости мелких деталей. Прибор для определения микротвердости состоит из механизма для вдавливания алмазной пирамиды под небольшой нагрузкой и металлографического микроскопа. В испытываемую поверхность вдавливают алмазную пирамиду под нагрузкой 0,05…5 Н.
Микротвердость измеряют путем вдавливания в образец (изделие) алмазного индентора под действием статической нагрузки Р в течении определенного времени выдержки т. Число твердости определяют (как и по Виккерсу) делением приложенной нагрузки в Н или кгс на условную площадь боковой поверхности полученного отпечатка в мм2.
Основным вариантом испытания является так называемый метод восстановленного отпечатка, когда размеры отпечатков определяются после снятия нагрузки. Для случая, когда требуется определение дополнительных характеристик материала (упругое восстановление, релаксация, ползучесть при комнатной температуре и др.) допускается проводить испытание по методу невосстановленного отпечатка. При этом размеры отпечатка определяют на глубине вдавливания индентора в процессе приложения нагрузки.
Практически микротвердость определяют по стандартным таблицам дня конкретной формы индентора, нагрузки Р и полученных в испытании размеров диагоналей отпечатка.
В качестве инденторов используют алмазные наконечники разных форм и размеров в зависимости от назначения испытании микротвердости. Основным и наиболее распространенным нконечником является четырехгранная алмазная пирамида с квадратым основанием (по форме подобна индентору, применяющемуся при определении твердости по Виккерсу).
Число микротвердости обозначают цифрами, характеризующими величину твердости со стоящим перед ними символом H с указанием индекса формы наконечника, например, Н□ =3000. Допускается указывать после индекса формы наконечника величину прилагаемой нагрузки, например: Н□ 0,196 =3000 — число микротвердости 3000 Н/мм2, полученное при испытании с четырех гранной пирамидой при нагрузке 0,196 Н. Размерность микротвердости (Н/мм2 или кгс/мм2) обычно не указывают. Если микротвердость определяли по методу невосстановленного отпечанка, то к индексу формы наконечника добавляют букву h (Н□h).
Соотношение значений твердости
При сопоставлении значений твердости, полученных разными методами, между собой и с механическими свойствами материалов необходимо помнить, что приводимые в литературных источниках таблицы или зависимости для такого сопоставительного перевода являются чисто эмпирическими. Физического смысла такой перевод лишен, так как при вдавливании paзличных по форме и размерам инденторов и с разной нагрузкой твердость определяется при совершенно различных напряженных состояниях материала. Даже при одном и том же способе измерения твердости значение сильно зависит от нагрузки: при меньших нагрузках значения твердости получаются более высокими.
Выше были рассмотрены основные методы контроля твердости. Существуют и другие методики контроля, которые основаны на косвенных измерениях значений механических свойств. Например электрические, магнитные, акустические и т.д. Все эти методы основаны на составлении экспериментальных корреляционных таблиц «измеряемый параметр — параметр механических свойств», где все параметры постоянны (химический состав металла, номер плавки, количество загрязнений), а меняются лишь табличные параметры. Такие методы на производстве практически не работают, т.к. например химический состав металлов по ГОСТам требуется в селекте, т.е. может быть в заданном пределе и меняться от плавки к плавке. Составление градуировочных таблиц на каждую партию металла — очень трудоёмкая работа. Pla пластик растворитель — https://www.dcpt.ru
Что нужно знать о ножевой стали?
Углеродистый металл с мелкими зернами в структуре легко затачивается, но легко подвергается коррозии. Клинки из порошковой стали обладают отличными режущими свойства, но тяжело поддаются доводке режущей части. Чтобы верно выбрать нож для конкретной цели, нужно знать несколько важных моментов о материале, из которого он изготовлен.
1. Существующие марки ножевой стали условно делят на 3 категории: премиум-класс, средний и нижний уровень .
Характеристики
Сфера применения
Премиум-класс
M390, ZDP-189, VG-10, Elmax, 154СМ, ХВ5, CTS-XHP, CPM S110V, CTS-204P, CPM S35VN
Высокая острота лезвия и жёсткость, прочность, упругость, ударная прочность, легкость заточки, формоустойчивость, износостойкость.
Медицинские и хирургические инструменты, ножевые клинки, ножи (в том числе складные) дорогого сегмента.
Средний уровень
4116, 14С28Т, 8Cr13Mov, D2, 440С, 420 НС, VG-1, AUS-8, Х12МФ, 9XC, 12С27 (Sandvic 12C27)
Хорошее соотношение цена/качество, относительно невысокая коррозионная стойкость, достаточная прочность, быстрая заточка режущей кромки.
Кухонные, охотничьи, туристические, складные, садовые и универсальные ножи.
Нижний уровень
AUS-6, 420, 440А, 65Г, 65Х13, 420J2
Низкое сопротивление ржавчине, быстро лопающиеся, сильно гнущиеся.
Кухонные, фиксированные, туристические, универсальные ножи и прочие режущие изделия низкого ценового сегмента.
2. Ножи из высокоуглеродистой нержавеющей стали, как правило, относятся к более высокому классу
• Высокоуглеродистая сталь — металлический сплав с содержанием углерода (С) от 0,6%. Его уровень влияет на твёрдость и прочность изделия. Так, например, в состав марки ZDP-189 (Япония) входит 2,9 — 3 % углерода, что позволяет при ее закалке получить до 69 HRC. • Нержавеющая — содержит более 10,5% хрома (Cr) и не менее 50% железа (Fe).
Ножи, изготовленные из сплава, объединяющего лучшие характеристики этих двух видов стали, прочны, тверды и коррозионностойки. Они устойчивы к механическим повреждениям, дольше сохраняют заточку и устойчивы к окрашиванию.
Чаще всего клинки из высокоуглеродистой нержавеющей стали содержат в составе сплава дополнительные элементы, такие как кобальт (Co), молибден (Mo), ванадий (V) и другие, что положительно влияет на качественные характеристики материала, увеличивая твердость и режущие способности лезвия между заточками.
3. Стоит отметить, что для определённых категорий колюще-режущих инструментов, очень высокая твёрдость не является преимуществом.
В частности, универсальные, туристические и ножи для дайвинга ценятся минимальной склонностью к коррозии и простотой заточки, что предполагает меньшее содержание углерода. Такие клинки имеют твердость ниже 60 HRC, но они достаточно надежны и хорошо переносят ударные нагрузки. Режущая кромка не будет сильно деформироваться, и их можно заточить «на коленке».
Как определить твердость ножа?
Показатель твердости ножевой стали демонстрирует характеристики изделия и качество его закалки.
Твердость определяют по шкале Роквелла HRC. Для контроля применяются портативные и стационарные твердомеры. Ознакомиться с подробным описанием главных отличий данных приборов можно в статье «В чём разница между портативными и стационарными твердомерами?».
Твёрдость стали качественных клинков
Тип ножа | Твёрдость |
Кухонные, универсальные, туристические | от 48 до 57 HRC |
Охотничьи | от 55 до 60 HRC |
Хирургические | от 58 до 62 HRC |
Топоры | от 62 до 70 HRC |
Для измерения уровня твёрдости ножа можно использовать ультразвуковые и универсальные твердомеры серии ТКМ. Высокоточный прибор ТКМ-459C оперативно выполнит контроль стали, не оставляя видимого отпечатка на поверхности.
Диапазон измерений твердости по Роквеллу С составляет 20-70 HRC.
Для работы с клинками подойдет комплект поставки, включающий ультразвуковой датчик типа «А» и/или «Н».
Изготовление самодельного сверла
При необходимости можно провести изготовление сверла из каленой стали. Среди основных рекомендаций по проведению подобной работы отметим:
- Подбираются стержни, которые изготавливаются из сплавов вольфрама и кобальта. В народе подобный металл называют победитом. В сравнении с обычным сверлом подобный вариант исполнения характеризуется повышенной устойчивостью к износу.
- Для обработки заготовки нужно закрепить ее в небольших тисках. В противном случае провести работу будет довольно сложны.
- Для затачивания подобной поверхности требуется алмазный камень. Обычный не выдержит длительную работу.
- Торцевая поверхность затачивается таким образом, чтобы получилась поверхность, напоминающая плоскую отвертку. После этого режущие кромки затачиваются для получения острого наконечника.
Для того чтобы снизить степень обрабатываемости поверхности проводится добавление масла. За счет этого обеспечивается длительная обработка по причине уменьшения силы трения и снижения температуры.
Самодельные сверла по каленке
В заключение отметим, что обработка каленой стали должна проводиться исключительно при применении специальных инструментов. Для работы требуется сверлильный аппарат, так как ручной не позволит получить требуемое отверстие.
Если вы нашли ошибку, пожалуйста, выделите фрагмент текста и нажмите Ctrl+Enter.
Легко! Любое победитовое сверло возьмет такую сталь. Можно и алмазное использовать, если нет под рукой победитового.
Если по условиям эксплуатации допустимо, чтобы участок, где нужно отверстие, может не иметь закалки, то можно локально прогреть это место, чтобы сделать отпуск и потом просверлить отверстие в этом месте уже обычным сверлом.
Ну, есть ещё плазменные, лазерные, электроэрозионные и другие методы обработки материалов, но это уже для тех, у кого есть под рукой соответствующее оборудование.
Сообщение митяй » 09 ноя 2011, 22:12
Да нах того хиндерера с его фиксаторами! Так буду ходить!
То есть даже если просверлить отверстие(нужного диаметра и не отпустить железку перегревом), то основные трудности начнутся потом — с нарезкой резьбы. На фиг, на фиг. Это уже в будущем, если надумаю плашку менять на самодельную, то тогда уже и насверлю нужных отверстий, и резьбу в них посажу — а потом уже и закалить можно будет.
Читать также: Схема подключения светильника через выключатель
Зато тема получилась насыщенная на полезные советы.
Сообщение kuhuk » 10 ноя 2011, 02:13
Сообщение Aleks » 10 ноя 2011, 09:48
kuhuk Высоко — это выше 56. 57. Да и то смотря к чему.
Ну ты же помнишь смертоубийственный кинжалище, помишь, как я засверливал через две втулки для соосности отверстие в хвосте. При таком раскладе у меня твердосплав достаточно быстро бы ушел в небытие. А вот быстрорезом аккуратненько с минимальными оборотами и с грамотной смазкой взял. Долго, нудно, с постоянным подтачиванием, но осилил. Не перегрел, не сжог, а именно просверлил. А ведь там было около 53 единиц! Твердосплавом было бы гораздо быстрее и проще, но в тех условиях на тех биениях патрона он бы и нескольких секунд не продержался. Так что возможно ХОРОШИМ быстрорезом сделать отверстие. Сложно, но можно. Твердосплавом проще.
А вот резьба — в тако отверстии — это действительно проблемища.
Методы измерения твердости
Все методы определения твердости металлов используют механическое воздействие на испытуемый образец – вдавливание индентора. Но при этом не происходит разрушение образца.
Метод определения твердости по Бринеллю был первым, стандартизованным в материаловедении. Принцип испытания образцов описан выше. На него действует ГОСТ 9012. Но можно вычислить значение по формуле, если точно измерить отпечаток на образце:
HB=2P/(πD*√(D 2 -d 2 ),
- гдеР – прикладываемая нагрузка, кгс;
- D – окружность шарика, мм;
- d – окружность отпечатка, мм.Шарик подбирается относительно толщины образца. Нагрузку высчитывают предварительно из принятых норм для соответствующих материалов:сплавы из железа — 30D 2 ;медь и ее сплавы — 10D 2 ;баббиты, свинцовые бронзы — 2,5D 2 .
Условное изображение принципа испытания
Схематически метод исследования по Роквеллу изображается следующим образом согласно ГОСТ 9013.
Метод измерения твердости по Роквеллу
Итоговая приложенная нагрузка равна сумме первоначальной и необходимой для испытания. Индикатор прибора показывает разницу глубины проникновения между первоначальной нагрузкой и испытуемой h –h
Метод Виккерса регламентирован ГОСТом 2999. Схематически он изображается следующим образом.
Математическая формула для расчета:HV=0.189*P/d 2 МПаHV=1,854*P/d 2 кгс/мм 2 Прикладываемая нагрузка варьируется от 9,8 Н (1 кгс) до 980 Н (100 кгс). Значения определяются по таблицам относительно измеренного отпечатка d.
Метод считается эмпирическим и имеет большой разброс показаний. Но прибор имеет простую конструкцию и его можно использовать при измерении крупногабаритных и криволинейных деталей.
Измерить твердость по Моосу металлов и сплавов можно царапанием. Моос в свое время предложил делать царапины более твердым минералом по поверхности предмета. Он разложил известные минералы по твердости на 10 позиций. Первую занимает тальк, а последнюю алмаз.
После измерения по одной методике перевод в другую систему весьма условен. Четкие значения существуют только в соотношении твердости по Бринеллю и Роквеллу, так как машиностроительные предприятия их широко применяют. Зависимость можно проследить при изменении диаметра шарика.
d, мм | HB | HRA | HRC | HRB |
2,3 | 712 | 85,1 | 66,4 | — |
2,5 | 601 | 81,1 | 59,3 | — |
3,0 | 415 | 72,6 | 43,8 | — |
3,5 | 302 | 66,7 | 32,5 | — |
4,0 | 229 | 61,8 | 22 | 98,2 |
5,0 | 143 | — | — | 77,4 |
5,2 | 131 | — | — | 72,4 |
Как видно из таблицы, увеличение диаметра шарика значительно снижает показания прибора. Поэтому на машиностроительных предприятиях предпочитают пользоваться измерительными приборами с однотипным размером индентора.
Если вы нашли ошибку, пожалуйста, выделите фрагмент текста и нажмите Ctrl+Enter.
Твердостью металла называют его свойство оказывать сопротивление пластической деформации при контактном воздействии стандартного тела-наконечника на поверхностные слои материала.
Испытание на твердость – основной метод оценки качества термообработки изделия.
Определение твердости по методу Бринелля. Метод основан на том, что в плоскую поверхность под нагрузкой внедряют стальной шарик. Число твердости НВ определяется отношением нагрузки к сферической поверхности отпечатка.
Метод Роквелла (HR) основан на статическом вдавливании в испытываемую поверхность наконечника под определенной нагрузкой. В качестве наконечников для материалов с твердостью до 450 HR используют стальной шарик. В этом случае твердость обозначают как HRB. При использовании алмазного конуса твердость обозначают как HRA или HRC (в зависимости от нагрузки).
Твердость по методу Виккерса (HV) определяют путем статического вдавливания в испытуемую поверхность алмазной четырехгранной пирамиды. При испытании измеряют отпечаток с точностью до 0,001 мм при помощи микроскопа, который является составной частью прибора Виккерса.
Метод Шора. Сущность данного метода состоит в определении твердости материала образца по высоте отскакивания бойка, падающего на поверхность испытуемого тела с определенной высоты. Твердость оценивается в условных единицах, пропорциональных высоте отскакивания бойка.
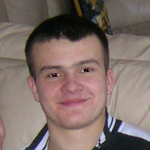
Эта тема закрыта для публикации ответов.