Состав
Мы можем назвать три основных семейства широко используемых волокон:
- бывшие целлюлозные волокна: полученные карбонизацией таких материалов, как бумага или вискоза;
- ex-PAN волокна: разработаны с 1960-х годов с использованием PAN в качестве прекурсора. Они широко используются в качестве арматуры в композитах. В настоящее время используются два типа волокон: высокопрочные волокна с большим удлинением при разрыве и волокна с высоким модулем Юнга ;
- ex-brais волокна: изготовлены из ароматических остатков от перегонки нефти или угля.
Волокна, полученные химическим осаждением из паровой фазы из предшественника углерода, такого как бензол, имеют различные свойства и области применения и обычно называются « углеродными нановолокнами ».
Углеродное волокно — это материал с очень высоким содержанием углерода (более 90% по массе). На атомном уровне волокно состоит из полиароматических углеродных листов, уложенных друг на друга по структуре, которая может быть очень близка к структуре графита , но также может быть более неупорядоченной, чем графит (турбостратный углерод, в котором стопка углеродных листов содержит дефекты). Уровень графитации волокон зависит от используемого прекурсора, а также от используемого метода производства. Расположение стопок углеродных листов составляет микроструктуру углеродных волокон, это также зависит от предшественника углерода и от процесса синтеза.
Получение
Рис. 1. Структуры, образующиеся при окислении ПАН-волокна
УВ обычно получают термической обработкой химических или природных органических волокон, при которой в материале волокна остаются главным образом атомы углерода.
Эта обработка состоит из нескольких этапов. Первый из них представляет собой окисление исходного (полиакрилонитрильного, вискозного) волокна на воздухе при температуре 250 °C в течение 24 часов. В результате окисления образуются лестничные структуры, представленные на рис. 1.[прояснить] После окисления следует стадия карбонизации — нагрева волокна в среде азота или аргона при температурах от 800 до 1500 °C. В результате карбонизации происходит образование графитоподобных структур. Процесс термической обработки заканчивается графитизацией при температуре 1600-3000 °C, которая также проходит в инертной среде. В результате графитизации количество углерода в волокне доводится до 99 %. Помимо обычных органических волокон (чаще всего вискозных и полиакрилонитрильных), для получения УВ могут быть использованы специальные волокна из фенольных смол, лигнина, каменноугольных и нефтяных пеков.
Общая информация
Данная статья описывает основные аспекты метода усиления конструкций углеволокном, а если точнее – технологию внешнего армирования строительных конструкций композитными материалами на основе углеродных волокон. Данный материал служит для ознакомления с основами данной технологии, вариабельностью применяемых материалов, но не может использоваться в качестве технологического, или проектного руководства в виду своей поверхностности и обобщенности.
Усиление конструкций углеволокном – относительно новый для России метод – первые реализованные в нашей стране объекты датированы 1998 годом. Заключается этот метод в наклеивании на поверхность конструкции высокопрочного углеволокна, воспринимающего на себя часть усилий, тем самым повышая несущую способность усиленного элемента. В качестве клея применяются специальные конструкционные адгезивы (связующее) на основе эпоксидных смол, либо минерального вяжущего. Благодаря высоким физико-механическим характеристикам углеволокна, повысить несущую способность конструкции можно практически без потери полезного объема помещений и увеличения собственного веса здания – толщина усиливающих элементов обычно составляет от 1 до 5 мм.
Следует понимать, что «углеволокно» — это материал (например, как бетон), а не конечное изделие. Из углеволокна изготавливают целый набор материалов, некоторые из которых применяются в строительстве – углеродные ленты, ламели и сетки.
В подавляющем большинстве случаев усиление углеволокном применяется для железобетонных конструкций – это обусловлено высокими технико-экономическими показателями реализации таких проектов. Однако, данная технология применима и к металлическим, деревянным и каменным зданиям и сооружениям.
Сильные и слабые стороны
Углеродная ткань обладает массой преимуществ по сравнению со стеклопластиком и другими материалами. Стоимость ее выше, поскольку производится по сложной многоступенчатой технологии с использованием дорогостоящих добавок на специальном оборудовании.
Достоинства карбоновой ткани:
- Небольшой вес по сравнению с металлами.
- Высокая термостойкость: выдерживает без деформации и потери свойств подогрев до 2000 °C.
- Безопасность: при ударах крошится, а не рассыпается на острые осколки.
- Демпфирующая способность: карбон отлично гасит вибрацию.
- Высокая теплоемкость.
- Высокая степень упругости, прочности на разрыв.
- Декоративный внешний вид.
Если сравнивать с металлом или стекловолокном, то у ткани из углеродного волокна обнаруживаются недостатки:
- Уязвимость к точечным ударам.
- Сложность ремонта царапин, трещин, сколов.
- Неустойчивость к ультрафиолету: выгорает под солнечными лучами, поэтому нуждается в лакированном или эмалевом защитном покрытии.
- Сложность, длительность и дороговизна изготовления.
- Подверженность коррозии в местах стыка с металлом, поэтому в этих участках требуются стекловолоконные вставки.
- Сложность и затратность повторного использования.
Усиление строительных конструкций — основные виды
Ниже перечислены основные виды работ, используемые при традиционном усилении:
- Устройство обойм и рубашек
- Усиление строительных конструкций установкой дополнительной арматуры
- Увеличение (наращивание) сечения элементов таких как: балок, ригелей, колонн, плит
- Устройство металлических обойм
- Установка разгружающих стоек, балок и рам
- Монтаж металлических порталов, рам, стоек
- Устройство предварительно напряженных затяжек, хомутов и раскосов
Усиление углепластиком можно отнести к внешнему армированию конструкций, способ и процесс усиления значительно проще, чем у традиционного способа, что позволяет не останавливать технологический процесс и уменьшает время на проведение ремонта.
Из-за простоты и удобства процесса усиления армирующим волокном в последнее время усиление углепластиком стало наиболее распространенным. Как уже упоминалось, недостатком нетрадиционного усиления является его стоимость — оно дороже, чем обычное усиление, но это только на первый взгляд — не стоит забывать, что долговечность и прочность материала увеличивает срок эксплуатации, а, следовательно, потенциально уменьшается количество последующих ремонтных работ и затрат на них.
Лучше сделать один раз, оценив долгосрочную перспективу вложений, и не думать об этом в дальнейшем.
История
Углеродные волокна представляют собой новое поколение высокопрочных волокон. Впервые производство углеродного волокна было предложено и запатентовано Томасом Алва Эдисоном в 1880 г. и использовать он его предложил в качестве нитей накаливания в электрических лампах. Однако, в широкое использование углеводородные волокна вошли только в 1960 годах, как наиболее подходящий материал для воздушной армии, особенно для изготовления ракетных двигателей поскольку обладают высокой термостойкостью. В последние десятилетия, углеродные волокна начали широко применяться в области аэронавтики, изготовлению спортивного инвентаря, производства автомобилей, в сфере строительства и, конечно же, музыкальных инструментов. Для получения углеродного волокна могут быть использованы специальные волокна из фенольных смол.
Углеродные волокна идеально подходят для изготовления продукции, где прочность, плотность и легкий вес являются главными характеристиками. Более того, оно также используется, когда высокая температура, химическая инертность и высокая демпфирование при производстве продукта, играет не менее важную роль. Благодаря химической инертности углеволокнистые материалы используют в качестве фильтрующих слоёв для очистки агрессивных жидкостей и газов от дисперсных примесей, а также в качестве уплотнителей и сальниковых набивок
Появления полиакрилонитрила (ПАН) и мезофазы (МП) считается важными этапом в истории углеродных волокон. Их структура и состав значительным образом влияют на свойства получаемых углеродных волокон. Не смотря на то что, основные процессы для производства углеродного волокна чем—то схожи, то для мезофазы и полиакрилонитрила используют различные условия обработки.
Условия транспортировки и хранения углеродного волокна
- Бобины должны храниться в крытых складских помещениях в упакованном виде, коробки должны находиться в горизонтальном положении.
- Рекомендуемые условия хранения.
- Температура: 0-40 °С. Хранение при минусовой температуре не рекомендуется.
- Влажность: 40-80%.
- Допускается перевозка в неотапливаемом транспорте при температуре до -30 °С.
- Во избежание конденсации влаги на поверхности. Перед использованием, нераспакованные бобины должны быть выдержаны не менее 48 часов при температуре от 20 до 30 °С и влажности от 40 до 80%.
- При правильных условиях хранения, производитель гарантирует сохранность свойств в течение 2 лет с даты производства.
Какого цвета карбон?
Карбон конечно черного цвета , поэтому что уголь, из которого он производится — изначально черный. Однако карбоновые поверхности можно окрашивать как в процессе производства, так и поверх готовой детали. Чаще всего карбон используют черного или белого цвета ( и оттенков серого) с сохранением оригинального рисунка плетения, чтобы показать, что деталь произведена из карбона.
Окрашивание углеродного компонента в цвет придает поверхности другой яркий вид. Существуют различные варианты получения цветного карбона. Когда окраска происходит в момент создания материала а не наносится поверх — то рисунок волокон сохраняется, что сигнализирует о том, что деталь карбоновая. Этот эффект особенно заметен на солнце.
Если красить поверх — то карбоновый рисунок пропадет. Конечно, если вам важны сами качества карбона а не внешний вид, то деталь можно красить, скрыв карбоновую структуру. Однако не стоит наносить бесцветный лак на карбоновые детали! Лак теряет цветостойкость и желтеет! В качестве альтернативы покраски также есть варианты с цветной смолой.
Отделка или герметизация карбоновых деталей
Конечно, это также имеет решающее значение для внешнего вида и качества прокладки карбоновых деталей, так называемого торца. Это защищает от вредных ультрафиолетовых лучей и других воздействий окружающей среды. Для герметизации вы можете выбрать один глянцевый лак или один из полуматовых лаков Clear.
Какая ткань из углеродного волокна самая прочная?
Для прямого сравнения возьмем тип холста 1 × 1 более естественный но не такой прочный, как материал корпуса 2 × 2 . Почему — это легко объяснить: если углеродные волокна натянуты, они снова попытаются выпрямиться. Однако благодаря особому расположению узора в формате полотняного переплетения волокна могут не просто натягиваться, но и прижиматься друг к другу. В результате ткань с трудом выдерживает сильное давление и разрыв. С плетением 2 × 2 корпуса достигается большая прочность на разрыв .
Стоимость усиления конструкций углеволокном
НАИМЕНОВАНИЕ РАБОТ |
МИНИМАЛЬНЫЙ ОБЪЁМ РАБОТ |
СТОИМОСТЬ РАБОТ, ВКЛ. МАТЕРИАЛЫ |
Проектирование усиления конструкций |
50 кв.м |
от 30 000 рублей |
1000 кв.м |
от 120 000 рублей |
|
5000 кв.м |
от 250 000 рублей |
|
Усиление углеродным волокном |
50 кв.м |
от 1 350 рублей/кв.м |
Примечание.
Во всех представленных выше таблицах указаны ориентировочные расценки на соответствующие работы. Для более точной оценки стоимости работ потребуется детальная информация по Вашему объекту. Чтобы уточнить стоимость работ оформите заявку на нашем сайте, закажите обратный звонок, либо позвоните по контактному номеру телефона: +7 (499) 391-19-35.
Это интересно: Правильное снятие плафона в салоне авто
Греющее углеволокно
Основа для нагревательного кабеля может быть различной, в данном случае это углеродная нить.
Углеволоконный греющий кабель – например, кабель для пола, знаком большинству потребителей. Основное отличие от аналогов: токопроводящий полимер на углеродной основе. Плюсы греющего УВ-кабеля: тонкий и прочный, простой в монтаже и пригодный к эксплуатации в любой среде – в бетоне, под плиткой, ламинатом, линолеумом и на стенах. Выделяет в 3 раза больше тепла, а электроэнергию экономит примерно в два раза, служит дольше аналогов. Теплые полы на основе углеволоконного кабеля модульным методом все более популярны.
Кованый углерод:
Forged Carbon (кованый углерод) один из типов карбона, Lamborghini разработала композит из углеродного волокна, который впервые был использован в Lamborghini Sesto Elemento. В отличие от обычных материалов из углепластика, Forged Carbon основан не на длинных, а на укороченных и прессованных пластиковых волокнах. Структура Forged Carbon очень похожа на камуфляж .
Феррари или льняной карбон:
Это карбон, который по структуре напоминает полотно — Canvas (полотняное переплетение 1 × 1), которое является ближайшей доступной углеродной тканой структурой. Пересечение систем нитей создает узор шахматной доски. Эта углеродная структура в основном используется в автомобилях Ferrari.
Исторический
Первое применение углеродных волокон было при разработке пряжи для ламп накаливания. Джозеф Свон произвел первые волокна в 1860 году. В первую очередь это были волокна из карбонизированной бумаги, затем он улучшил качество углеродных нитей, используя углеродные хлопковые волокна. С 1879 года Томас Эдисон использовал высокотемпературные карбонизированные бамбуковые волокна. В 1880 году Льюис Латимер усовершенствовал процесс Томаса Эдисона для получения надежных углеродных волокон, в результате чего время работы лампы составило несколько сотен часов. С 1892 года от электрического освещения будет отказано в пользу освещения путем нагрева ламп накаливания для общественного освещения, а производство углеродных проводов будет прекращено на несколько десятилетий.
В 1958 году Роджер Бэкон (en) хотел определить тройную точку атомов углерода путем нагревания при высокой температуре в дуговой печи, он наблюдал образование углеродных нитей. Он продолжал изучать образование этих нитей, чтобы прийти к запатентованному методу подготовки. Процесс был основан на карбонизации вискозных волокон , его использовала компания Union Carbide (чья углеродная ветвь позже стала Graphtec ). Однако механические свойства этих волокон были ограничены из-за низкого содержания углерода. В 1960 году Акио Шиндо произвел углеродные волокна более высокого качества из полиакрилонитрила (волокна ex-PAN). В тот же период Ричард Миллингтон усовершенствовал процесс производства волокон из вискозы. Их высокое содержание углерода (99%) и их хорошие механические свойства позволили рассматривать их использование в качестве арматуры в композитных материалах. В течение этого десятилетия проводились исследования по поиску новых прекурсоров углерода для получения волокон. Они приводят к процессам производства углеродных волокон из нефтяного пека.
В 1963 году У. Ватт, Л. Н. Филлипс и У. Джонсон (Royal Aircraft Establishment в Фарнборо, Хэмпшир) разработали процесс изготовления композитных материалов. Компания Rolls-Royce использует этот процесс для производства лопаток компрессора для своих двигателей RB211 . Однако эти композиты чувствительны к ударам ( например, столкновениям с птицами), что ограничивает их использование в аэронавтике. В тот же период правительство Японии очень активно поддерживало развитие промышленного производства углеродных волокон, и несколько компаний развили это направление ( Toray , Nippon Carbon , Toho Rayon , Mitsubishi ). Япония становится лидером в области углеродных волокон из PAN.
Мировой спрос на углеродные волокна.
В 1970-х годах на мировом рынке доминировала компания Union Carbide, которая использовала процесс Toray. Компания Courtaulds — единственный крупный британский поставщик. Эта компания останется важным поставщиком композитных материалов для применения в спорте до конца 80-х годов. Соединенные Штаты и Европа также поощряют такие компании, как BASF , Celanese или Akzo, к развитию промышленного производства углеродных волокон.
Распределение мирового производства углеродного волокна по странам в 2015 г.
С конца 1970-х годов многие разработки привели к производству волокон с механическими свойствами, подходящими для множества различных применений. В основном различают высокомодульные волокна и высокопрочные волокна. Спрос на композитные материалы постоянно растет, в основном это связано с авиационной, оборонной и ветроэнергетической отраслями. Это привело к появлению на этом рынке новых игроков, таких как Китай или Южная Корея. В последнее время необходимость замены прекурсоров углерода из ископаемых ресурсов прекурсорами на биологической основе привела к исследовательской деятельности в области волокон на основе лигнина . Композитные волокна также были разработаны с использованием углеродных нанотрубок в качестве структуры.
Рекомендации
- Swan KR Сэр Джозеф Свон и изобретение электрической лампы накаливания , Лондон, Longmans, Green and Co., 1946, стр. 21–25
- Льюис Х. Латимер, Патент США 252386 Процесс производства угля
- Р. Бэкон, Рост, структура и свойства усов графита , Журнал прикладной физики , т. 31, n ° 2, февраль 1960 г., стр. 283–290
- Р. Бэкон, Нитевидный графит и метод его получения , Патент США 2,957,756.
- Патент США № 3294489.
- Д.А. Бейкер, Т.Г. Риалс, Последние достижения в производстве недорогих волокон из лигнина , Journal of Applied Polymer Science , vol. 130, стр. 713-728, 2013
- ↑ и
- ↑ и П. Дельхес, П. Олри, Углеродные волокна и композиционные материалы , L’Act. Чим. , полет. 295-296, с. 42-46, 2006 г.
- ↑ и
- ↑ и P.J. Walsh, Carbon Fibers , ASM Handbook , vol. 21, 2001, с. 35-40
- X. Бертран, Поведение в окислительной среде углеродно-углеродного композита для структурных приложений при температуре от 150 до 400 ° C в гражданской авиации , диссертация Университета Бордо I, 2013 г.
- Льюис, И.С., Процесс производства углеродных волокон из мезофазного пека , Патент США No. 4032430, 1977 г.
- Дифендорф, RJ; Риггс, Д.М., Формирование оптически анизотропных пеков , Патент США No. 4208267, 1980 г.
- Дж. Д. Бакли, Д. Д. Эди, Углерод-углеродные материалы и композиты , Noyes Publications , 1993
- W. Fang, S. Yang, X.-L. Ван, Т.-К. Юань, Р.С. Сан, Производство и применение углеродных волокон на основе лигнина (LCF) и углеродных нановолокон на основе лигнина (LCNFs) , Green Chemistry , vol. 19, стр. 1794-1828 , 2017
- С. Отани, Ю. Фукуока, Б. Игараси, С. Сасаки, Патент США 3461082, 1969 г.
- Ю.-Л. Ли, И. А. Кинлох, А. Х. Виндл, Прямое прядение волокон из углеродных нанотрубок в результате химического синтеза из газовой фазы , Наука , т. 304, стр. 276, 2004 г.
- Р. Хаггенмюллер, Х. Х. Гомманс, А. Г. Ринзлер, Дж. Э. Фишер, К. И. Вини, Выровненные одностенные углеродные нанотрубки в композитах методами обработки расплава , Химическая физика Letters , vol. 330, стр. 219, 2000 г.
- Б. Виголо, А. Пенико, К. Кулон, К. Саудер и др. , Макроскопические волокна и ленты из ориентированных углеродных нанотрубок , Наука , т. 290, стр. 1331, 2000
(fr) Эта статья частично или полностью взята из статьи в Википедии на английском языке под названием « Углеродные волокна » ( см. список авторов ) .
Приложения
О других проектах Викимедиа:
Углеродное волокно , на Викискладе?
Внешняя ссылка
«Углеродные волокна» , на сайте технических публикаций инженера .
Углерод |
|||||||||||
---|---|---|---|---|---|---|---|---|---|---|---|
Аллотропные формы углерода |
|
||||||||||
Производные аллотропных форм |
|
||||||||||
Ископаемый углерод |
|
||||||||||
Другие формы |
|
||||||||||
Изотопы |
|
Волокна |
|||||||
---|---|---|---|---|---|---|---|
Натуральный ( Список ) |
|
||||||
Синтетический |
|
||||||
|
- Химический портал
- Физический портал
- Портал промышленного производства
- Материаловедческий портал
Преимущества углеродного волокна
Можно с уверенностью сказать, что не совсем дорогие композиты из углеродных волокон, будут способны внести большой вклад для различных видов технологий, в том числе для технологий, который только начинают развиваться и также не стоит забывать особое значение этого волокна в человеческой жизни. При изготовлении автомобилей, автобусов, поездов, самолетов, кораблей и т.д, начинают появляться панели и конструкции с довольно легким весом, что постепенно может привести к экономии и всемирному уменьшению употребления энергии. Недорогое углеродного волокна является национальной целью, к реализации ряда технологических прорывов производства.
Метод аппликации (ручная оклейка)
Сделать карбон своими руками можно методом оклейки, который включает пять основных этапов:
- Тщательная подготовка оклеиваемой поверхности: зашкуривание, обезжиривание, скругление углов.
- Нанесение адгезива.
- Приклеивание углеткани с пропитыванием эпоксидной смолой с отвердителем.
- Сушка.
- Покрытие защитным лаком или краской.
Наполнители для смолы используют как для придания декоративности, так и для предотвращения стекания смолы с вертикальных поверхностей.
Необходимые материалы
- Адгезив для фиксации углеткани на поверхности.
- Ткань из углеволокна, которую укладывают на смолу послойно, с прикатыванием твердым валиком.
- Эпоксидная смола средней вязкости с отвердителем (иногда она используется в качестве адгезива).
- Защитный лак. Лучше всего для защиты от царапин подходит полиуретановый. Нужно выбирать водостойкий и светостойкий. Он не помутнеет. Для высокого блеска в качестве финишного покрытия можно использовать акриловый лак.
Смолу наносят 2-3 раза с промежуточной сушкой и шлифовкой.
Этот метод отличается от традиционного изготовления карбоновых изделий по моделям нанесением адгезива, а не разделителя для легкого съема получившегося полуфабриката.
Компания 3М предлагает даже самоклеющееся углеполотно, но работа с ним требует хороших навыков.
И карбон остается на оклеиваемой детали, упрочняя ее. Такое производство карбона чаще всего используется для оклеивания бампера, приборной панели и пр.
Технические характеристики карбоновых волокон
Для углеродных волокон основными механическими характеристиками являются предел прочности на растяжение σв, предел прочности на единицу объема, а также модуль упругости, определяющий эластичность и способность работать на изгиб.
Механические свойства сильно зависят от ориентации волокон, то есть они анизотропны, хотя в плетении Pane и Twill эффект анизотропии свойств проявляется меньше. Технические характеристики, как правило, приводятся для продольного направления.
Углеродные волокна обладают следующими механическими характеристиками по сравнению с армирующими металлическими, стекловолокном и полимерными волокнами.
Волокно (проволока) |
ρ, кг/ м³ |
Тпл, °C |
σB, МПа |
σB/ρ, МПа/кг*м-3 |
Алюминий |
2 687 |
660 |
620 |
2 300 |
Асбест |
2 493 |
1 521 |
1 380 |
5 500 |
Бериллий |
1 856 |
1 284 |
1 310 |
7 100 |
Карбид бериллия |
2 438 |
2 093 |
1 030 |
4 200 |
Углерод |
1 413 |
3 700 |
2 760 |
157 |
Стекло E |
2 548 |
1 316 |
3 450 |
136 |
Стекло S |
2 493 |
1 650 |
4 820 |
194 |
Графит |
1 496 |
3 650 |
2 760 |
184 |
Молибден |
0 166 |
2 610 |
1 380 |
14 |
Полиамид |
1 136 |
249 |
827 |
73 |
Полиэфир |
1 385 |
248 |
689 |
49 |
Сталь |
7 811 |
1 621 |
4 130 |
53 |
Титан |
4 709 |
1 668 |
1 930 |
41 |
Вольфрам |
19 252 |
3 410 |
4 270 |
22 |
Например, параметры углеродных волокон Toray из полиакрилата (PAN) c высокой прочностью на растяжение High Modulus Carbon Fiber.
Волокно (fiber) |
Модуль упругости (msi) |
Предел прочности (ksi) |
M35J | 50 | 683 |
M40J | 57 | 398 |
M40J | 55 | 640 |
M46J | 63 | 611 |
M50J | 69 | 597 |
M55J | 78 | 583 |
M60J | 85 | 569 |
Существует взаимосвязь — чем выше предел прочности, тем ниже модуль упругости.
Что влияет на технические характеристики карбоновых композитов
При подборе материала очень важно найти оптимальный баланс между характеристиками, подбирая слои, направление волокна, метод плетения и плотность. Механические свойства готовых композитов определяются следующими параметрами:
- тип карбонового волокна и смолы,
- тип плетения, ориентация волокон,
- соотношение волокон (т.е. плотность полотна) и смолы в композиции,
- плотность, однородность, пористость и пр.
Ну и не забываем про опыт и навыки работы с композитами.
Автор Ирина Химич
При копировании материалов не забывайте, что у каждого текста есть автор. Поэтому при добавлении материала на свой сайт не забывайте ставить индексируемую ссылку на первоисточник!!!
Армирование углеволокном
Исходный вид углеволокон – это тончайшая микрофибра, пригодная для армирования и монолитного бетона, и эпоксидного гелькоата. Толщина фибры – 5-10 микрон, длина волокон различна. Укрепляют углеволокном и отделочные поверхности, и несущие элементы в массиве.
Что касается закладного армирования, то оно выполняется в строительстве «традиционно» — переработанными УВ-продуктами: карбоновым текстилем различных видов, холстами, ровингом, стержневой арматурой на полимерных смолах. Последний вариант – пример работы карбоновых волокон не в качестве микроармирования для несущего элемента, но для надежного крепежа и фиксации. По качествам прочности (в том числе на сдвиг и скручивание) и фиксации углеволоконная фибра во много раз превосходит стеклянную, полимерную и металлическую.
Усиление перекрытия углеволокном
Перекрытие, так же как и любую другую несущую конструкцию здания, можно усилить сеткой, ламелью или лентой из углеволокна методом наклейки в напряженной зоне (по расчету, но чаще всего это нижняя грань плиты в центре пролета). Цель усиления перекрытия – повысить несущую способность по изгибающим моментам. Это относится и к сборным элементам – усиливают и монолитные и пустотные плиты по сходной технологии. В приопорных зонах для элементов перекрытий любого вида минимизируют развитие наклонных трещин – для этого применяют углеродные ленты или сетки в виде U-образных хомутов. Возможно усиление не только ж/б, но и металлического, и деревянного перекрытия.
Усиление деревянных балок углеволокном
Деревянные элементы можно усилить обмоткой карбоновым полотном, ровингом, углетканью любого вида – в виде лент, лоскутов, фрагментов на наиболее нагруженных участках. В частности, это узел опирания и центральный растянутый участок балки, а в стропильных деревянных системах – соединения и фиксация арок и ферм к подстропильному брусу (мауэрлату). Оклеивание выполняют на эпоксидных смолах, также содержащих микроволокно углерода.
Шпатлевка с углеволокном
Акриловые окраски, венецианские декоративные штукурки, полимерный пол – все это примеры отличных, эстетичных и модных отделок. Но без армирования в массе многие декоры слишком хрупки и непрочны, поэтому применение углеволокна в качестве фибры, а также закрепление стыков и швов панелей и облицовок под окраску с применением углеволоконного текстиля (ленты, полотна) – идеальное решение. Применяют карбоновые ткани и при финишной отделке, и для выравнивания стен при штукатурке. Отдельная широкая сфера применения — авто-тюнинг и ремонт.
Внешнее армирование углеволокном
Системы внешнего армирования (СВА) применяют для всех видов строительных конструкций и для практически всех стройматериалов (древесина, железобетон, металлы, камень). Цель внешнего усиления при восстановлении и реконструкциях – устранить последствия коррозий и разрушений вследствие природного негатива и долгой эксплуатации. Перспективны СВА и в сейсмостроительстве. Методика внешнего армирования позволяет не изменять структуры и схемы конструкций, по сути это поверхностное усиление суперпрочными углеродными сетками, тканями, ламелями и другими продуктами на основе углеволокна.
При новом строительстве СВА включают обмотку несущего элемента (балка, армопояс, стойка, лента и т.д.) углеродным полотном или толстым ровингом, далее заливают защитный слой из бетона на тонком наполнителе (кварцевый мелкофракционный песок). Один из плюсов метода – практически полное исключение коррозии внутренней стальной арматуры: внешнее усиление и защитный пескобетонный слой заключает элемент в прочную обойму. Но основная цел СВА – усиление прочности и снижение веса строительных конструкций и элементов.
Вы слышали про углепластик или карбон?
Углепластик, или карбон (от англ. carbon), — это современный, легкий, но очень прочный материал, применяемый в аэрокосмической отрасли, и незаменимый во многих отраслях промышленности (производство спортивного инвентаря, медицинского оборудования, автомобилестроение и так далее). Благодаря возможности его переработки и технологии производства карбоновые детали могут иметь различную форму и габаритные размеры.
На стадии проектирования (расчета на прочность композитов) задаются параметры будущего материала, и за счет определенной ориентации волокон в полимерной матрице, например, в эпоксидной смоле, достигается оптимальное соотношение веса и прочности. Карбон используется в тех изделиях, где его отношения веса к прочности имеет существенное значение. Это в свою очередь повышает экономическую выгоду, потому что при сочетании в себе множества достоинств данный материал стоит недешево, что связано с особенностями технологии его производства и немалой долей ручного труда, непосредственно в процессе изготовления деталей из карбона. Некоторые изделия из углепластика нелегко массово производить и поэтому такое производство обходится очень дорого. Если бы можно было сказать, что углеродное волокно имеет какие-либо недостатки, это были бы издержки производства.
Этот материал стал настолько популярен, что существует не мало других синтетических материалов, которые имитируют настоящее углеволокно. Тем не менее, имитации часто представляют собой только пластик, выполненный в виде структуры углеродного волокна или различные пленки. Carbon Composites использует только высококачественные углеткани.
Как получают углеродное волокно ?
Углеродные волокна изготавливаются путем термической обработки тончайших нитей углерода с последующей карбонизацией (т. е. нагрев в азотной среде) и графитизацией (т. е. насыщение углеродом для повышения прочности). Углеродные ткани (углеткани) получают путем плетения нитей или лент.
А то, что обычно называют углепластик или карбон, представляет собой материал, состоящий из углеродных тканей, лент, волокон, и при соединении с полимерной матрицей (эпоксидной смолой или другими полимерами) под действием тепла, давления и/или в вакууме образуется композитный материал, который является одновременно прочным и легким. Это делает его особенным.
Изделия из карбона от компании Carbon Composites
В последние годы производство изделий из углепластика заметно выросло, и во многих отраслях всё активнее применяется этот по-настоящему уникальный материал. Покупателям компании Carbon Composites доступны изделия из карбона на заказ, выполненные из композитных материалов, максимально подходящих под выбранный проект. Вы можете заказать карбоновые детали высокого качества, обладающие всеми преимуществами данного материала и изготовленные в строгом соответствии с технологией
Немаловажное преимущество изготовления изделий карбона на заказ — в том, что они могут формоваться как единое целое, что позволяет избежать появления слабых мест в конструкции (которые неизбежно возникают в металлических конструкциях из-за формирования изгибов и соединений). Карбон позволяет создавать цельные изделия, в которых нагрузка равномерно распределяется по всей площади
А поверхность из многочисленных нитей в составе углепластика очень красиво переливается на свету.
Используйте все преимущества углепластика (карбона) — материала будущего — заказывая продукцию в компании Carbon Composites.
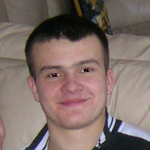
Эта тема закрыта для публикации ответов.